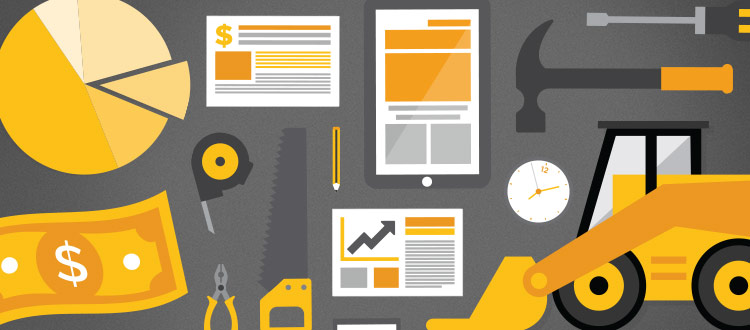
The best method for allocating overhead in construction is a way that’s fair. After all, the idea is to allocate (or, distribute) costs that each job shares responsibility for — meaning the job either caused or benefited from the cost.
But, the costs should also be proportional to that responsibility. Figuring out how to strike that balance is the art of overhead allocation.
Think of your construction projects as a bunch of college roommates. Assuming they all have identical bedrooms and equal kitchen privileges, it’s fair to split the rent evenly.
Beyond that, it might get complicated. Let’s say one of them doesn’t watch cable, so they divide the bill among those that do. They all pitch in for milk and bread — but they don’t all use them equally.
In our roommate analogy, paying more than your share of groceries might be small potatoes, but in construction overhead, we’re talking about many thousands — if not millions — of dollars. You want these numbers as accurate as possible. That’s why various methods exist, with different levels of complexity. It's also why contractors should involve their construction CPAs to determine the best method for their business. Your overhead allocation methods should fit your particular situation.
Choosing an Allocation Basis
Depending on the type of work your construction company does, and where the bulk of your overhead comes from, you have numerous options for what to base your allocation on. These include:
- direct labor costs
- direct material and subcontract costs
- direct labor hours
- total direct costs
- and much more
The idea is that you choose this part of your method based on what makes sense for your company.
A labor-intensive contractor might look at using field hours or payroll costs. This lets them assign more of their payroll-related overhead to jobs with more payroll activity. Sounds logical, right? At the same time, this might not be the best way for them to allocate all of their overhead costs.
Let’s look at an example.
A coatings contractor might allocate most of their overhead by labor hours, but as an exception, they could also choose to allocate just their consumable supplies overhead (like roller heads and towels) based on their materials cost. The thinking would go like this: How many consumable materials they use may or may not have much to do with their job hours, but the more paint they use on a job, the more roller heads they can bet they’re going through.
That means contractors aren’t necessarily locked into using just one allocation basis or method for allocation — especially if they have the guidance of a CPA experienced in construction and the assistance of construction accounting software that’s built to be flexible.
Choosing an Allocation Method
Along with choosing what you’ll use to allocate your overhead, you’ll need to choose how you want to calculate it. You can think of two different categories of methods, either:
- a rate of costs or revenues, or
- a proportion between your jobs
Remember, each method tries to understand how your job activity relates to your overhead. In broad strokes, the difference is where you look for the answer: at the job level or at a company level.
In selecting a rate of costs or revenues method, a contractor is only looking at one job at a time. They’re counting on a fairly predictable relation between how much a job costs or brings in and how much overhead it incurs, so they use a predetermined percentage. With a proportion between jobs method, they look at each job’s share of a larger pie.
Where does that rate come from, and what’s the pie they’re sharing?
Let’s look at some examples of methods.
Rate of Total Direct Job Costs
A simple example of a rate allocation method would look at all of the direct costs for a project as one big number and estimate that its share of overhead should amount to roughly x% of those costs.
To find that magic percentage, the company might use history as a guide. They can choose to divide all overhead costs for the previous fiscal year by the total direct job costs in the previous fiscal year.
FY total direct job costs = $18,000,000
FY overhead costs = $2,000,000
$2,000,000 / $18,000,000 = 11.11%
If they and their CPA are confident in that rate being a good predictor going forward, they can apply that rate to all incoming job costs in order to estimate how much in overhead costs should be associated with that job’s bottom line. Those amounts would then go into a special category within their job cost structure, which they set up with their CPA.
Rate of Direct Job Costs
Alternatively, but using the same principle, our example contractor can use a method based on some direct job costs but not the total. If they decide that field labor costs are really what indicate whether their overhead costs are high or low, they might look just at that rate.
FY direct labor costs = $5,000,000
FY overhead costs = $2,000,000
$2,000,000 / $5,000,000 = 40%
Notice how their overhead allocation rate skyrocketed!
Won’t that mean the allocated amounts in their job costing will go through the roof? It actually won’t.
Here’s the trick: Under this method, our contractors would only apply this rate to certain job costs. In this case, since their rate is based on field labor, they’ll only apply it to incoming field labor costs. As a result, as long as their estimates are good, we would expect their allocation to be different with each method — but within the same ballpark.
Proportion of Direct Costs
For a generally more accurate overhead allocation method, contractors can track each overhead expense in their G/L and distribute the totals proportionally across their jobs. There are numerous ways to determine this proportion, including using direct costs again.
Say that a job represents 25% of our imaginary company’s direct job costs. This method would assign 25% of the company’s overhead G/L accounts for a given period to that job. The remaining 75% would go to each of the other jobs proportionally in the same way. That’s why this type of method can be viewed as more accurate. If done correctly, 100% of every overhead expense that hits the G/L can be accounted for under one job or another.
A proportional method that uses G/L accounts also lets accounting professionals add complexity for finer-grain allocation control. With the help of their construction accounting software, contractors can choose to allocate only a portion from each overhead G/L account.
This can be helpful, for example, if you use an overhead allocation account for depreciation costs that your CPA doesn’t want to allocate.
Weighted Proportion of Direct Costs
Going further, they could choose have certain G/L expense accounts receive a greater or lesser proportion of allocated costs, using a weight factor. Imagine a labor-intensive contractor has two jobs that each represent 15% of their grand total of direct costs. One was truly labor intensive, so it incurred a lot of overhead.
In contrast, the other used a lot of subcontract labor without much impact on overhead. This contractor might decide it doesn’t make sense for both jobs to receive the same allocated amount. Now what?
What they can do is use a higher weight factor (e.g., 2.0) on the field labor G/L account to give labor-intensive jobs a boosted proportion of overhead costs. They can also use a lower weight factor (e.g., 0.5) on expense accounts like subcontracts, materials, etc. That way, high-expense but low-overhead jobs don’t get an unfair amount of allocation. It artificially inflates or deflates the costs that make up the job total and the overall total — but only for the purposes of giving a percent to allocate. So instead of 15% each, they might calculate allocating 19% to one and 11% to the other.
Combination
Among the numerous ways to allocate overhead in construction fairly and accurately, methods aren’t necessarily exclusive to one another.
As long as a company tracks different types of overhead, it might also choose to allocate them differently. Our coatings contractor from before wanted to allocate their consumable supplies overhead by a proportion of direct materials costs. What about payroll overhead? They might estimate it with a rate of direct labor costs. For the rest of their overhead, they might choose a third method — as long as they’re not duplicating any allocation.
Remember the old adage: measure twice, allocate overhead once.
There are seemingly endless possibilities for how you can spread out your overhead among your projects for more accurate project and financial reporting. But don’t let that intimidate you. Simply schedule some time with your construction CPA to discuss the best options for you, given your software features and the way you do business.
For more control over your allocation, check out a free product tour of FOUNDATION® construction accounting software.
Share Article
Keep on current news in the construction industry. Subscribe to free eNews!
Our Top 3 YouTube Videos
Learn about our software more in depth with product overviews, demos, and much more!
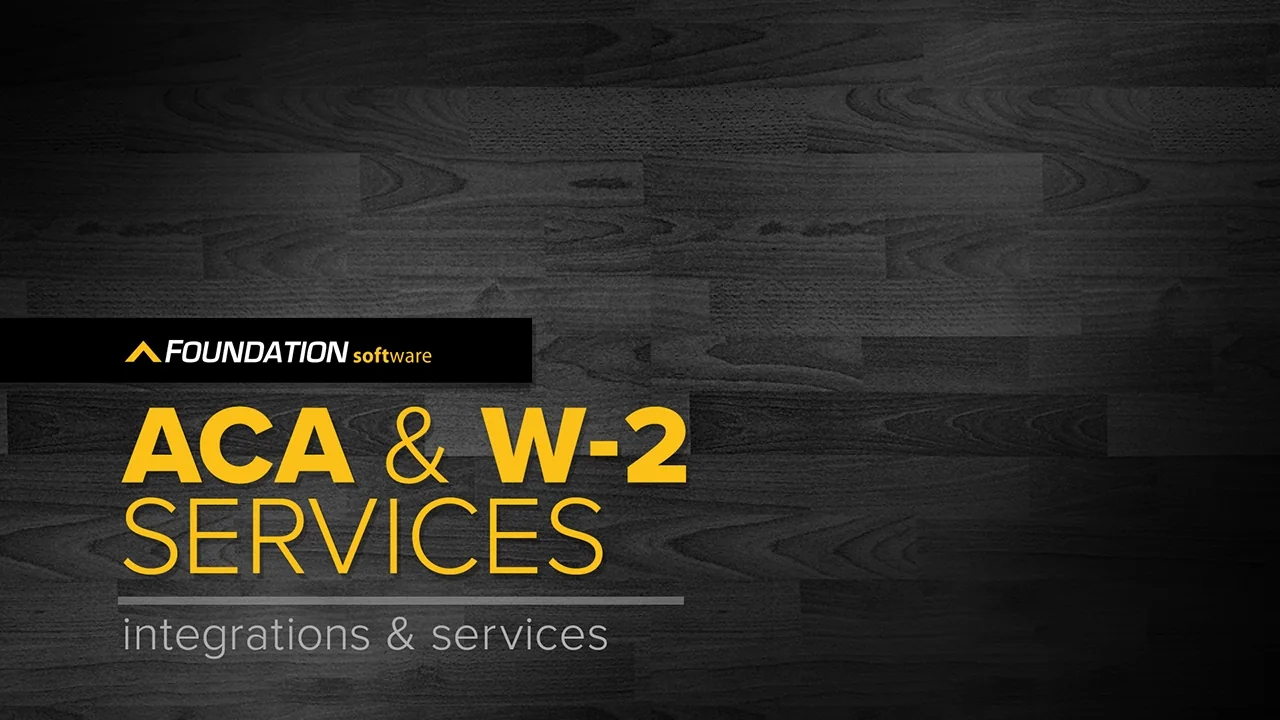
Our ACA reporting & e-filing services include official 1094-C and 1095-C IRS reporting, optional e-filing (no applying for a TCC code required), mailing to your employees and experienced support to help you.
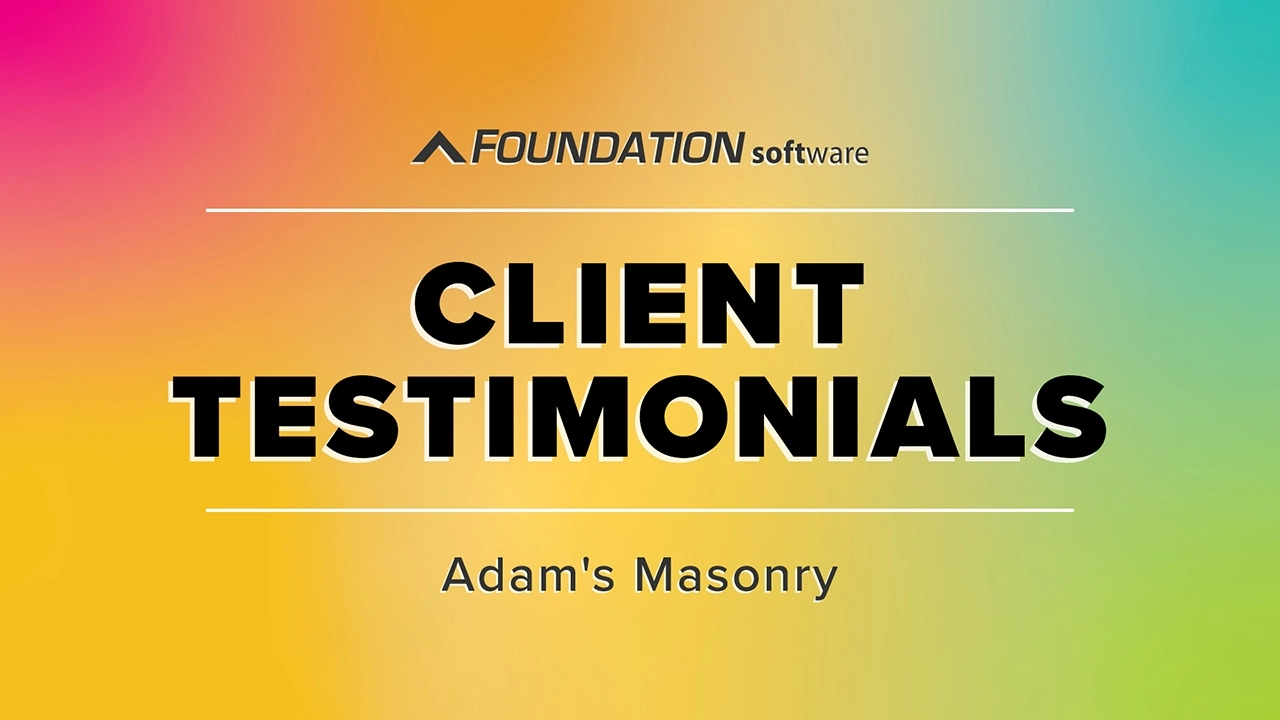
There are plenty of reasons to make FOUNDATION your choice for job cost accounting and construction management software — just ask our clients!
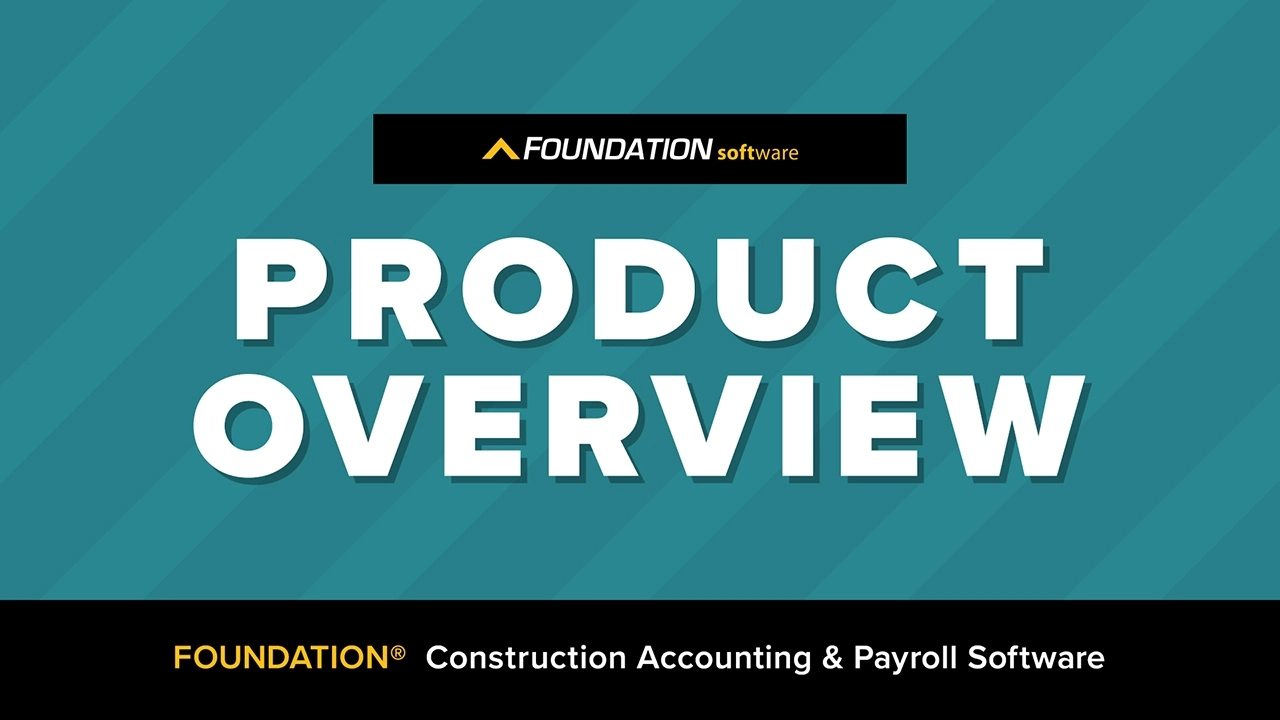
From job cost accounting software, to construction-specific payroll. Get an overview on your next all-in-one back-office solution.