
The impact construction tariffs are having on this industry is noticeable and contractors are finding themselves needing to rethink how they run their day-to-day operations and plan for the future.
Whether you’re a small contractor or running a large construction firm, statistically speaking, tariffs are increasing material costs.
From steel beams to lumber and everything in between, the decision to implement tariffs is creating many changes, both short-term and long-term.
Right now, contractors are dealing with price fluctuations. While the prices of some materials are stabilizing, others continue to change almost every day. This makes it tough for contractors to quote jobs accurately or maintain consistent pricing.
The good news?
There are ways to stay ahead of the game and keep your business thriving, even when the market throws you curveballs.
Key Takeaways About Construction Tariffs
- Recent construction tariff rates range from 10% to 25%
- Some construction materials increased in price by 20-40% since the imposition of tariffs.
- Overall project costs have risen 15-25%, causing profit margins to shrink by 5-10% for many construction firms.
- Market analysts predict steel prices will stabilize in the next 6-12 months and aluminum costs will continue to increase.
- US-based suppliers are adapting to more flexible pricing models.
- Construction-specific software solutions like FOUNDATION® help contractors track real-time material costs and update billing rates automatically.
Current State of Construction Tariffs
Experts are paying attention to how the newly proposed trade policies affect the construction industry because many building materials are often outsourced and imported from other countries.
Recent tariffs on various construction materials range from 10% to 25%. This creates a complex web of price adjustments that ripple through every aspect of construction projects.
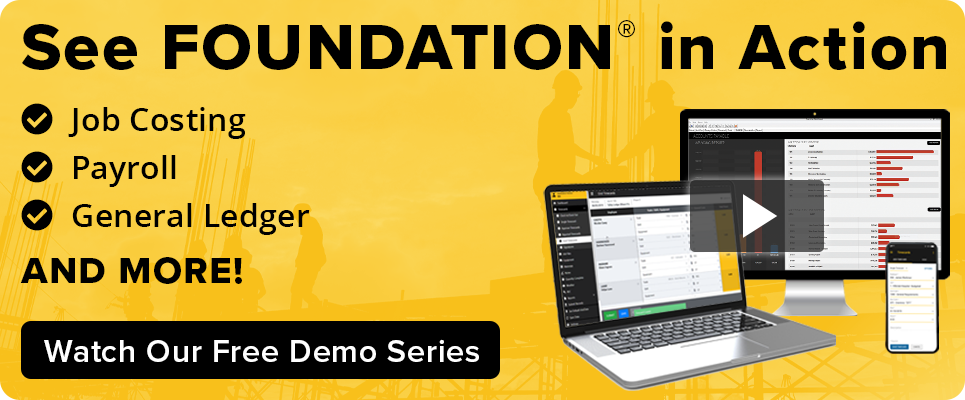
Key Construction Materials Affected
Imported steel and aluminum now have tariffs. Common steel construction materials like structural steel, rebar and metal roofing materials have seen price increases.
On average across the industry, many reported seeing the prices for these materials increase between 20% and 40% since tariff implementation.
Other key materials that contractors say have increased in price since the tariffs started include:
- Lumber, specifically for softwood
- Electrical components and wiring since they contain copper and aluminum
- Glass products
- Basic materials like fasteners and hardware because they often contain tariffed metals
Real Cost Impact on Projects
Financial changes related to the effects of tariff policies include things other than material cost increases.
Construction professionals reported that they are seeing a 15-25% rise in overall project costs. This translates to a change in bid accuracy and project timelines.
A typical commercial construction project that previously budgeted $1 million for materials might now require $1.2 million or more for the same scope of work.
The impact becomes particularly evident in fixed-price contracts, where contractors must absorb these unexpected cost increases.
Many construction firms report that when they look at their books, profit margins are shrinking by 5-10% due to tariff cost increases. This is creating a pressing need for new approaches to project planning and execution.
Looking Ahead: Tariff Trends and Predictions
The construction landscape continues to evolve as global trade policies shape material costs and availability.
Understanding both immediate and long-term trends becomes essential for construction professionals aiming to maintain profitable operations.
Market analysts and industry experts point to several key developments that warrant attention from construction firms planning their future strategies.
Short-term Outlook
In the immediate future, construction professionals can expect continued changes in prices across many building materials.
Statistically speaking, market indicators suggest prices for steel may stabilize somewhat over the next 6-12 months. However, when they do stabilize, historical data tells us that the new prices will be more expensive than pre-tariff prices.
Economic experts across the board say that aluminum costs look like they will continue to increase. There are modest increases projected through the year’s end.
Many contractors are turning to alternative, local sources. Although the prices for US-made materials are lower than current market prices, they often come with longer lead times. This requires additional planning for project schedules.
US-based material suppliers are starting to offer more flexible pricing models to help construction firms manage uncertainty. These new approaches include:
- Shorter quote validity periods
- Improved communication about upcoming price changes
- Option for price-lock agreements with deposits
- Sliding scale pricing based on order volume
- Risk-sharing contracts that distribute cost increases between supplier and buyer
This means several things for construction companies.
Contractors now have more tools to navigate material cost changes.
The shorter quote validity periods reflect real-time market conditions more accurately. Improved communication channels create transparency and allow firms to anticipate changes before they happen.
The newer options like price-lock agreements and risk-sharing contracts give construction firms ways to stabilize their project budgets. However, these often come with tradeoffs like upfront deposits or slightly higher initial costs.
This shift, while challenging, allows for more accurate project budgeting when handled properly.
Long-term Industry Changes
The construction industry faces many changes that will likely last beyond current trade policy fluctuations.
Domestic manufacturing capacity for essential construction materials will continue to expand. These changes will probably lead to more stable pricing. However, they may initially result in higher baseline costs as manufacturers recover their investment in new facilities.
Alternative materials and construction methods are gaining traction as contractors seek ways to find less costly materials that are still high quality.
Contractors say they will be turning to new, innovative building materials that weren’t previously a good option because of pricing concerns. For example, many builders are now choosing to use engineered wood products instead of steel in some applications.
More contractors are choosing to use technology across the industry as they look for better ways to manage material costs and project planning. Digital tools for material tracking, cost estimation and project management are becoming essential rather than optional.
How Software Makes a Difference
Contractors no longer have to cross their fingers and hope material prices stay put. Modern software puts contractors back in control of their numbers.
When tariffs change material prices, construction software steps in like a trusted assistant who never sleeps. Contractors can pull up real-time data that shows exactly how construction price changes affect their bottom line, and track additional costs that may not have been factored into the original estimate.
Staying connected with suppliers becomes a whole lot easier too. Contractors no longer find themselves drowning in a sea of emails and phone calls about price changes. They can use their software to track who’s offering what and for how long.
This kind of intelligence helps contractors stay one step ahead of tariff-related price hikes.
Having solid data makes all the difference. Instead of awkward conversations about why construction costs went up, contractors can pull up clear, professional reports that show exactly what changed and why.
Construction-specific accounting software turns potentially tense discussions into straightforward business conversations backed by real numbers.
FOUNDATION® Protects Your Bottom Line
Construction tariffs are creating a few challenges for contractors. Some contractors are struggling to maintain accurate bids and protect their profits.
Staying profitable in this environment requires more than just good business sense. It demands powerful software tools that can keep pace with real-time changes.
Contractors need software solutions that track material costs across multiple projects, analyze price trends and provide instant visibility into how costs from tariffs impacts their bottom line.
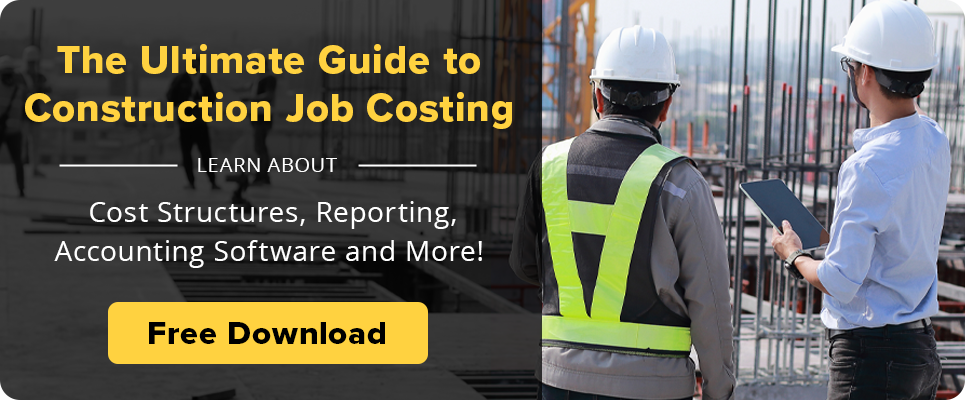
That’s where FOUNDATION’s comprehensive suite of accounting tools steps in to make a real difference.
The FOUNDATION® Time and Material module specifically helps contractors deal with tariff uncertainty.
The module tracks material costs in real-time and automatically updates billing rates when prices change. For contractors working on time-and-material contracts, this means never missing out on recovering increased costs.
The FOUNDATION® Unit Price Billing module takes things a step further. It offers contractors a way to handle price fluctuations in unit-price contracts.
When material costs change, the module automatically adjusts billing rates based on predefined rules and triggers. The system also tracks historical price changes, giving contractors valuable data for future bids and negotiations.
Most importantly, it helps construction firms maintain their profit margins even when material prices change unexpectedly.
Together, these FOUNDATION modules create a robust shield against construction tariff impacts.
Chat with a specialist to learn more!
Share Article
Keep on current news in the construction industry. Subscribe to free eNews!
Our Top 3 YouTube Videos
Learn about our software more in depth with product overviews, demos, and much more!
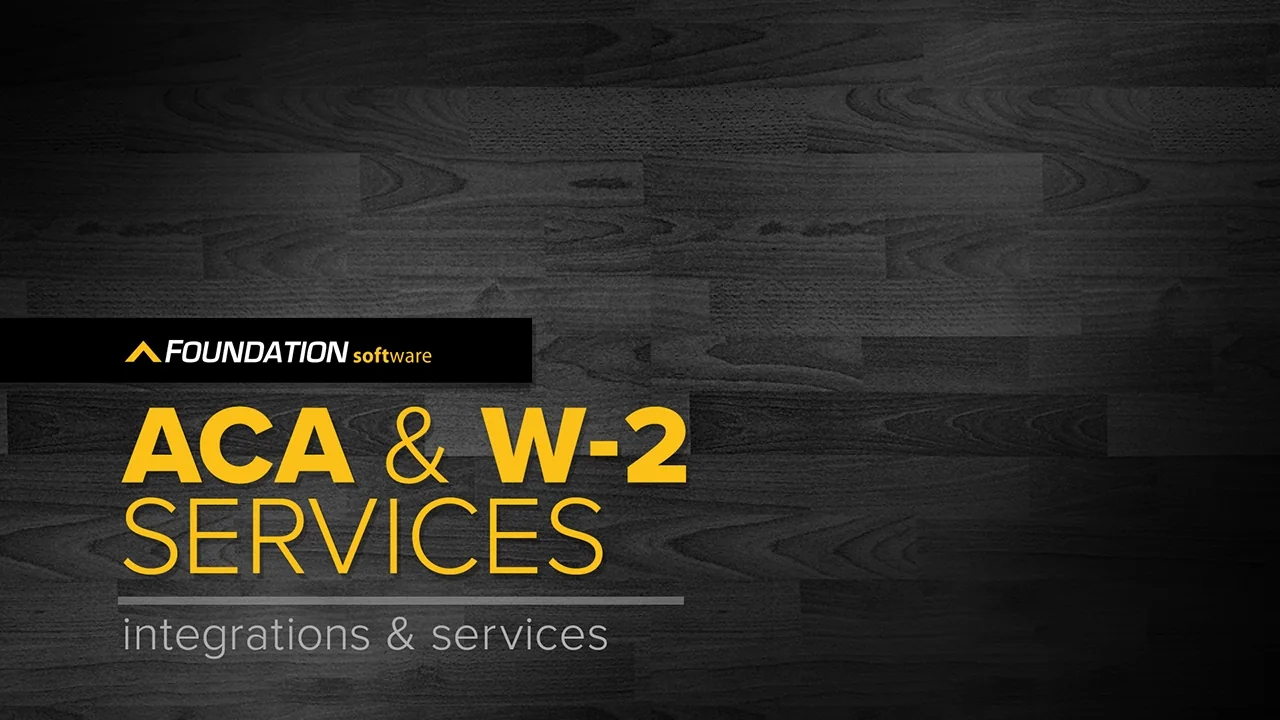
Our ACA reporting & e-filing services include official 1094-C and 1095-C IRS reporting, optional e-filing (no applying for a TCC code required), mailing to your employees and experienced support to help you.
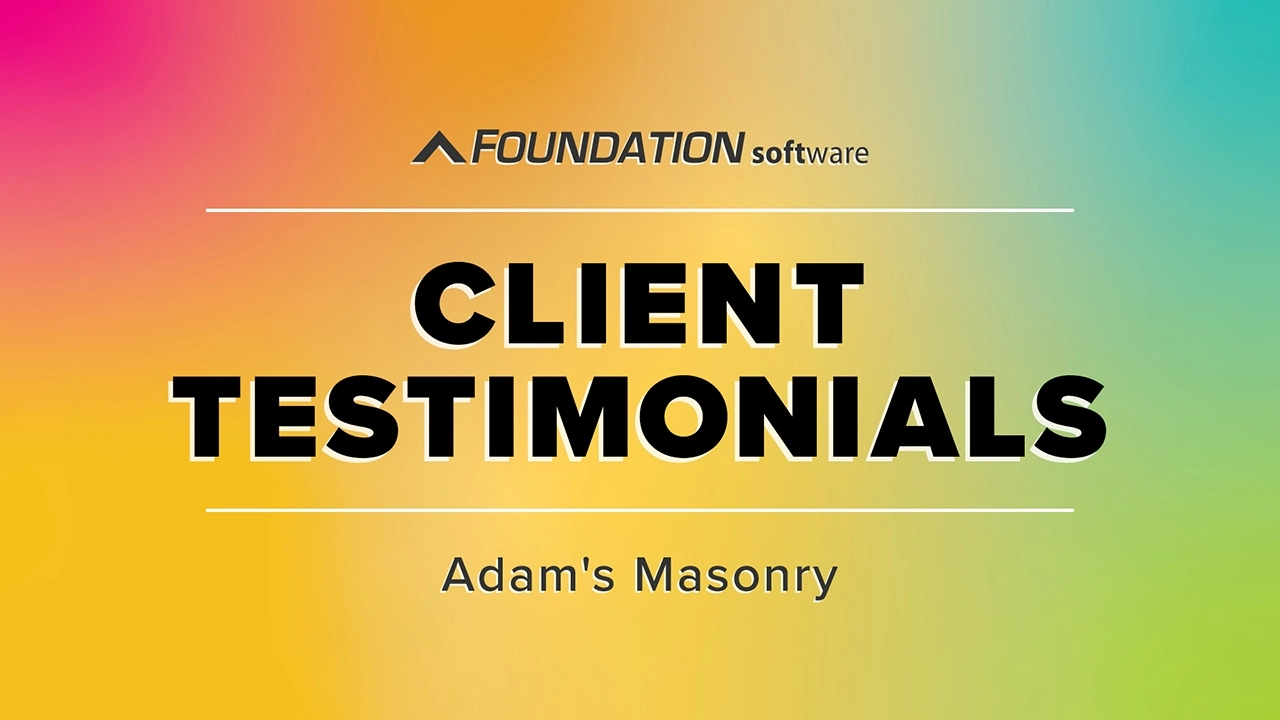
There are plenty of reasons to make FOUNDATION your choice for job cost accounting and construction management software — just ask our clients!
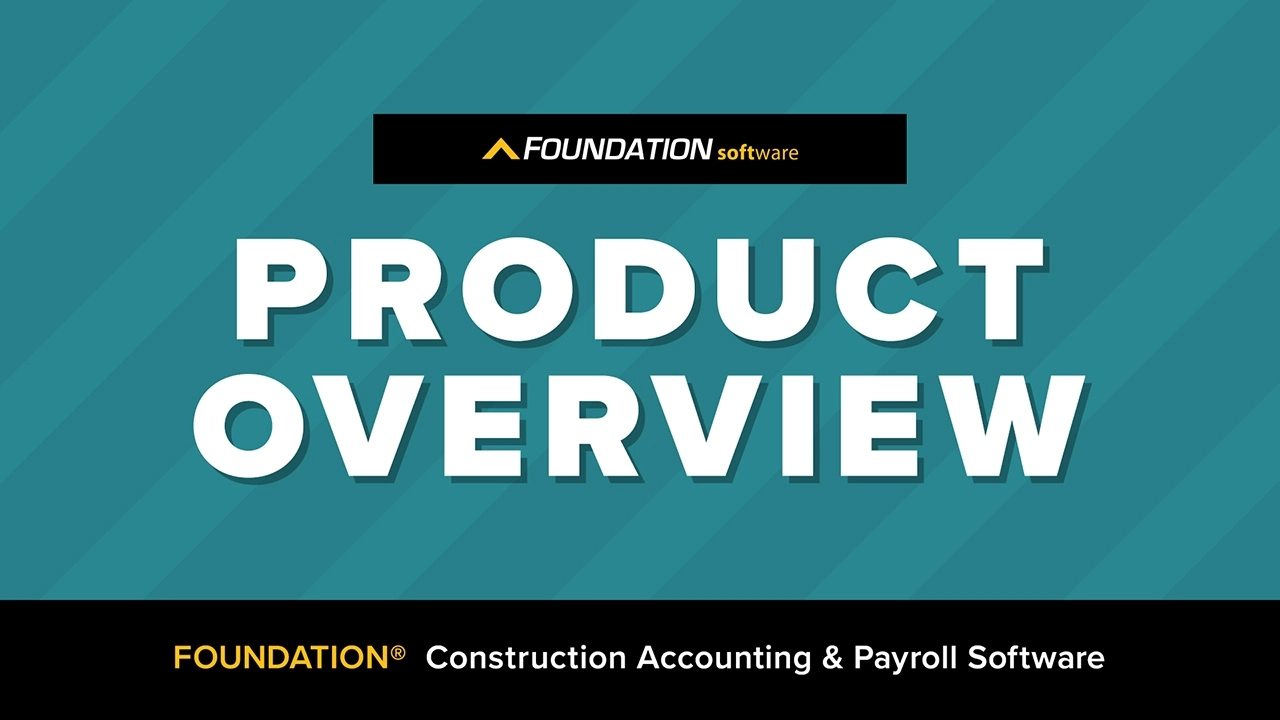
From job cost accounting software, to construction-specific payroll. Get an overview on your next all-in-one back-office solution.