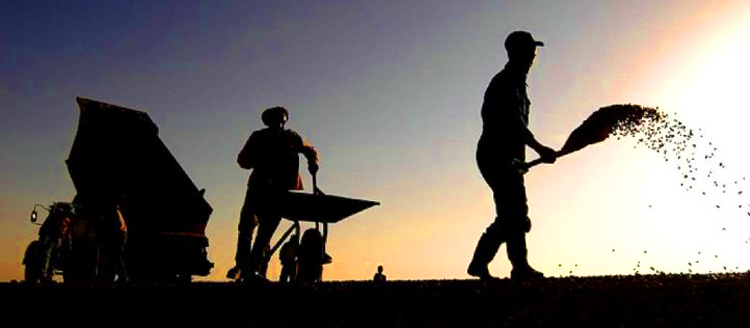
Ask any contractor what has the greatest impact on a job’s bottom line, and chances are the answer will be the same: labor productivity.
For general contractors managing multiple trades, specialty contractors, and commercial builders coordinating large crews, no other job cost comes close to providing such a variable for rewards and risks. Compared to other construction cost items such as materials and equipment, labor productivity typically accounts for 20-40% of project costs and can varyĀ based on project conditions.
Contractors need to see production reports to answer specific job questions, including:
- What is the quantity completed per man-hour?
- What is the actual versus estimated production rate?
- What will the projected cost for completing the project be based on the average production to date?
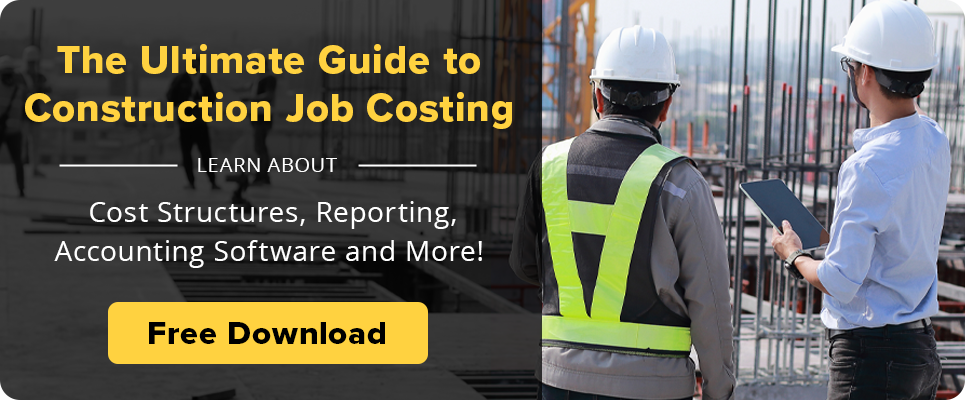
Check out our article about reporting for minority compliance.
Unfortunately, many contractors simply donāt have access to detailed production reporting. Without a sophisticated job-cost accounting software that offers features like:
- Real-time production tracking with mobile field data entry
- Automated productivity calculations and variance analysis
- Historical performance database for estimating
- Custom report generation by cost code, crew, or activity
Finding the True Production Rate
When contractors estimate the cost of a job, their labor costs are generally determined by what they believe their labor force can complete per labor hour. Industry-standard production rates vary by trade:
- Pipe installation: 8-12 feet per hour
- Concrete placement: 25-30 cubic yards per hour
- Steel erection: 1.5-2 tons per hour
- Drywall installation: 150-200 square feet per hour
For example, if a job requires 1,000 feet of pipe installation, a contractor may estimate it will take 100 labor hours to complete the work, with an estimated production rate of 10 feet per labor hour.
Of course, few jobs are that simple.
More often, they involve many different field activities, different labor crews, and different pay scales, all of which can affect a contractor’s production rates.
For example, imagine that a contractor is halfway through a construction project and finds that he is way behind schedule. Can he identify which field activity is behind? Does he know which crew is underperforming? If so, the job could be saved. If not, the fate of the job remains uncertain.
Using integrated payroll and field data, a good job-costing accounting program can provide contractors with specific, real-time production reporting. With Foundationās date-sensitive transaction data and flexible reporting, thatās not the only advantage.
Since contractors can reference their past production reports when bidding on similar jobs, their estimates are likely to be more accurate and their profits higher.
Whatās more, historical production reports help contractors identify their strengths and weaknesses, which means they can bid more aggressively on certain field activities or even back away on areas with lower production rates.
What Kind of Production Reports Should Contractors Use?
Just as no two construction companies are alike, no two contractors will likely require the same types of production reporting. The kind of jobs a contractor does, its labor force, and many other factors will determine how a company will want to see its production numbersāand how often.
A good construction-specific accounting program, therefore, should offer flexible reporting options. At a minimum, contractors should be able to produce the following reports:
- Labor Productivity Report. For every activity or phase, this report shows the number of units completed per labor hour.
- Labor Unit Cost Report. This report shows current labor costs per unit (e.g., for every foot of pipe laid). The costs can include labor costs only or labor and burden together.
- Unit Cost Report. Similar to the Labor Unit Cost Report, this report includes all current costs per unit of measure, adding material costs, equipment costs, etc.
- Projected Cost Analysis. Based on current costs per unit completed, this report shows what the projected final overall cost will be for a specific activity, as well as how many units are still needed for completion.
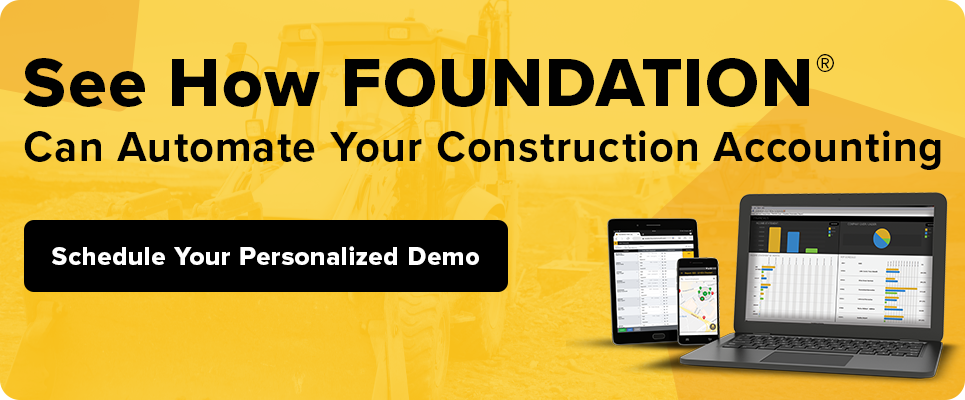
In addition to standard construction reports, Foundationās construction report designer empowers contractors to modify and even create their own custom reports.
Retrieving reports from a job-cost accounting system like Foundation is as easy as:
- Entering estimated costs, hours, and units for each field activity that needs to be entered into the system
- Entering costs and units as they occur
Using data already in the system, a world of production reporting is opened. That means no more guessing on where a job stands and no more guessing on productivity rates for similar job bids.
Best of all, by removing the guesswork on labor productivity, the rewards can go directly to the bottom line.
*A version of this article first appeared in Software Solutions.
Share Article
Keep on current news in the construction industry. Subscribe to free eNews!
Our Top 3 YouTube Videos
Learn about our software more in depth with product overviews, demos, and much more!
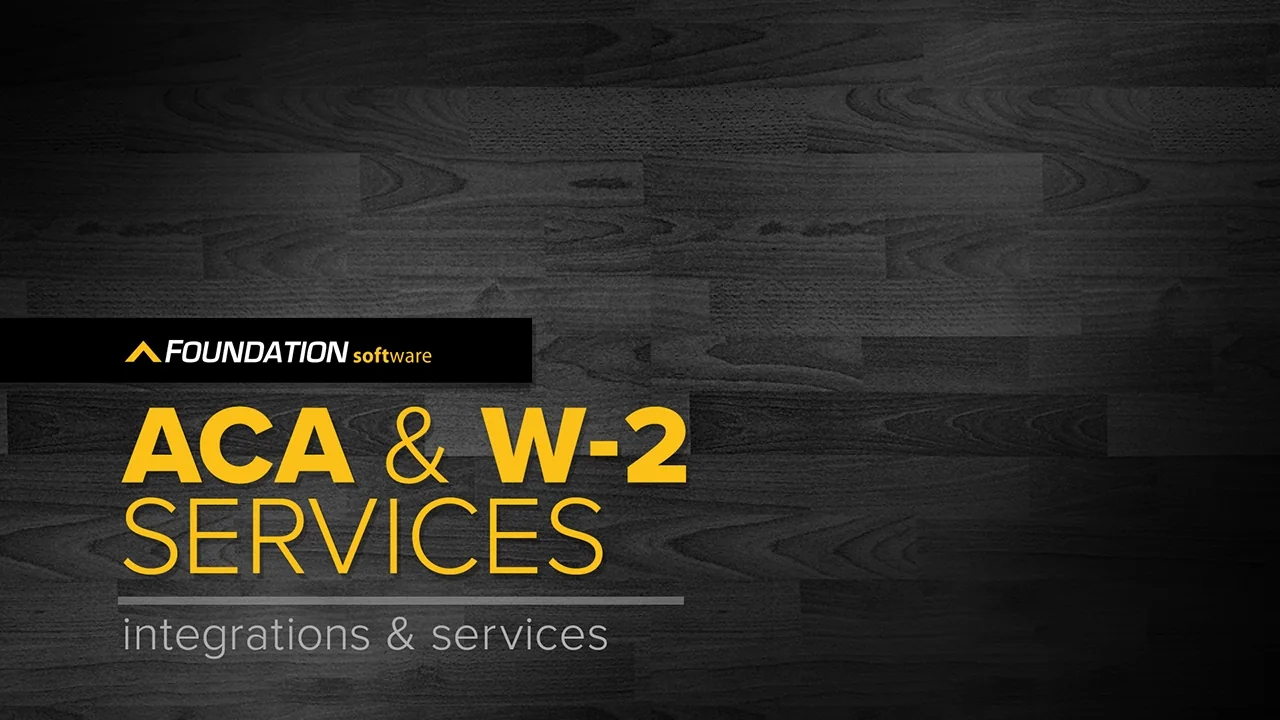
Our ACA reporting & e-filing services include official 1094-C and 1095-C IRS reporting, optional e-filing (no applying for a TCC code required), mailing to your employees and experienced support to help you.
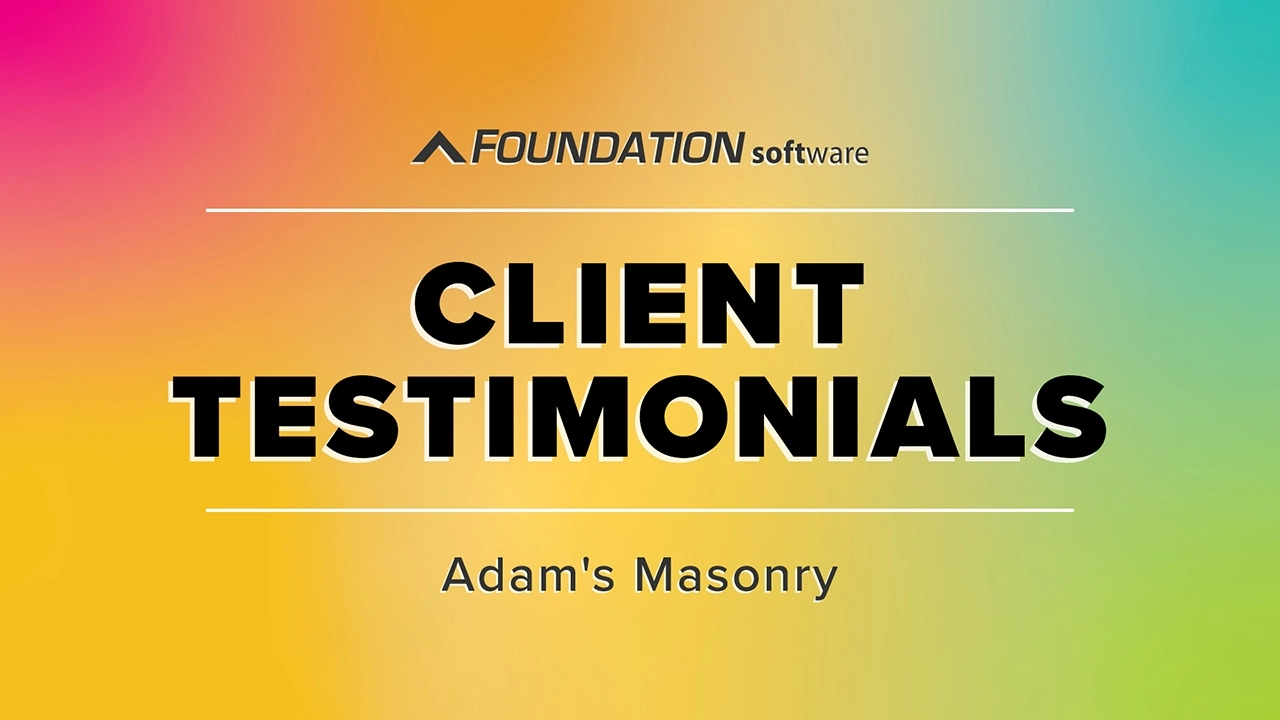
There are plenty of reasons to make FOUNDATION your choice for job cost accounting and construction management software — just ask our clients!
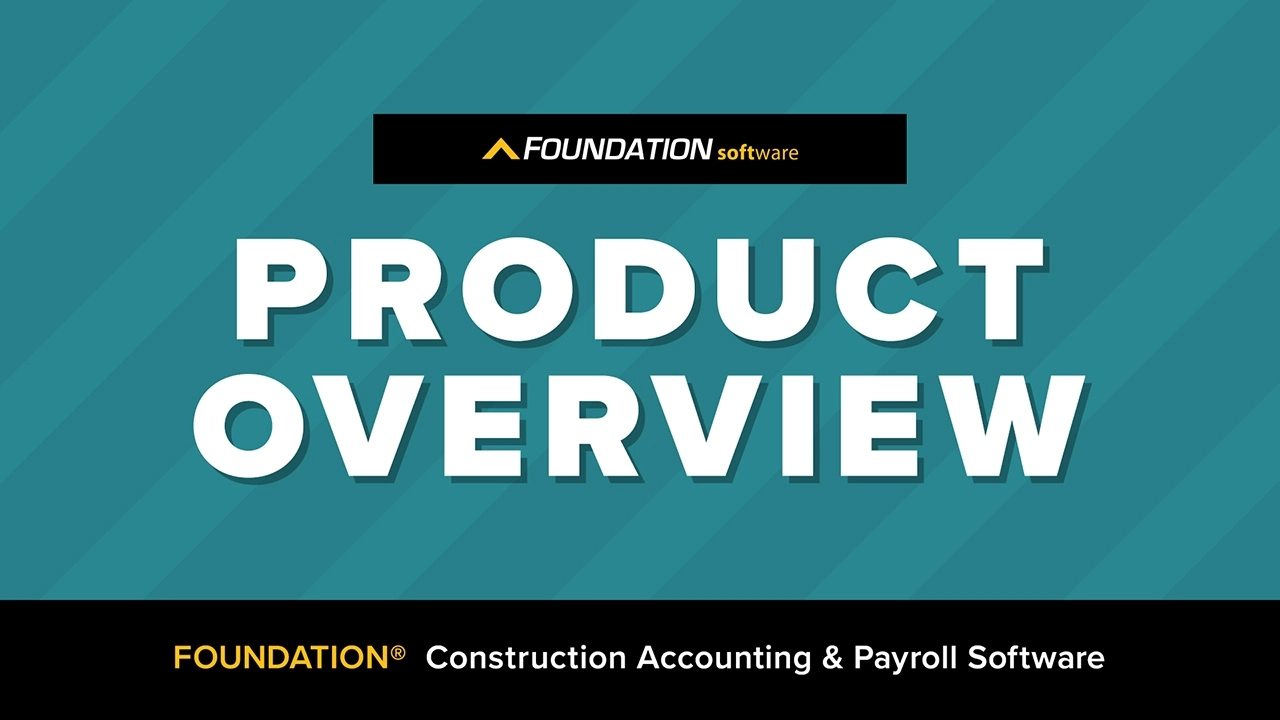
From job cost accounting software, to construction-specific payroll. Get an overview on your next all-in-one back-office solution.